জানু. . 29, 2025 04:47
The realm of industrial manufacturing has witnessed substantial evolution in recent years, with various sectors emphasizing sustainable and efficient production processes. One segment experiencing significant advancement is the zeolite manufacturing industry. Zeolites, known for their unique molecular structure and exceptional ion-exchange capabilities, have become indispensable in various applications ranging from environmental to industrial uses. They are pivotal in water purification, petrochemical processes, and even in agronomy, contributing to more eco-friendly solutions. Establishing a zeolite factory is both an art and a science, demanding meticulous planning, precise execution, and a commitment to quality.
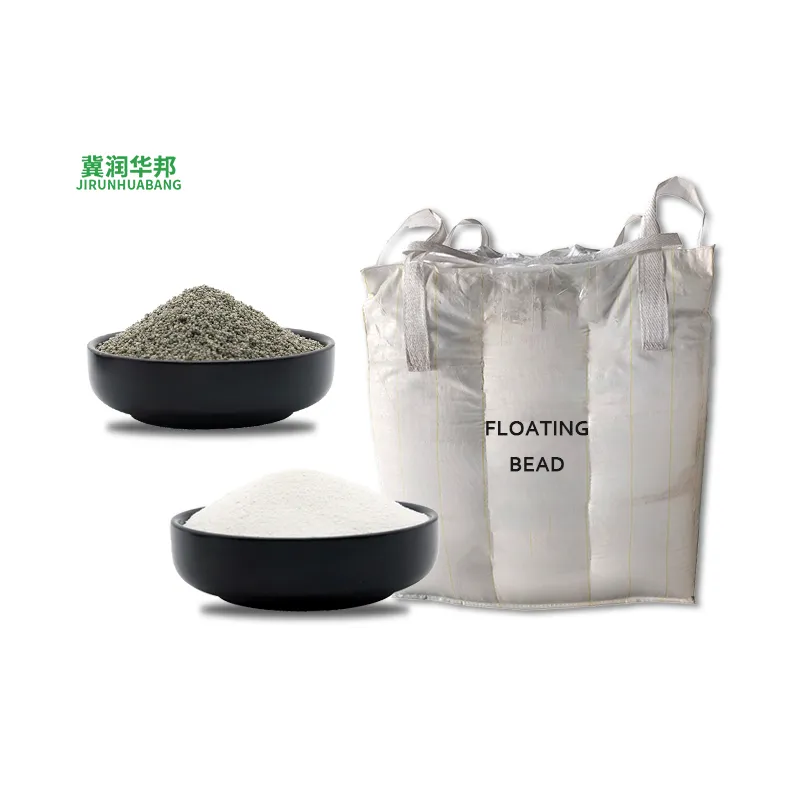
A critical aspect of launching a successful zeolite production facility is understanding the unique properties and applications of zeolites. Unlike typical materials, zeolites possess a microporous structure that allows them to function as molecular sieves. This intricate lattice enables them to selectively adsorb molecules based on size and polarity, making them invaluable in numerous commercial applications. One notable example is their use in catalysis. Industries can engineer zeolites to serve as efficient catalysts in hydrocarbon processing, facilitating cleaner fuel production with reduced emissions.
Selecting the right location for a zeolite factory is pivotal. A factory's site influences not only logistical considerations but also impacts its environmental footprint. Proximity to natural zeolite deposits is advantageous, reducing raw material transportation costs and supporting sustainability goals by minimizing carbon emissions. Furthermore, establishing a zeolite factory in a region with robust infrastructure, such as readily available utilities, skilled labor, and accessible transportation networks, is beneficial for seamless operations.
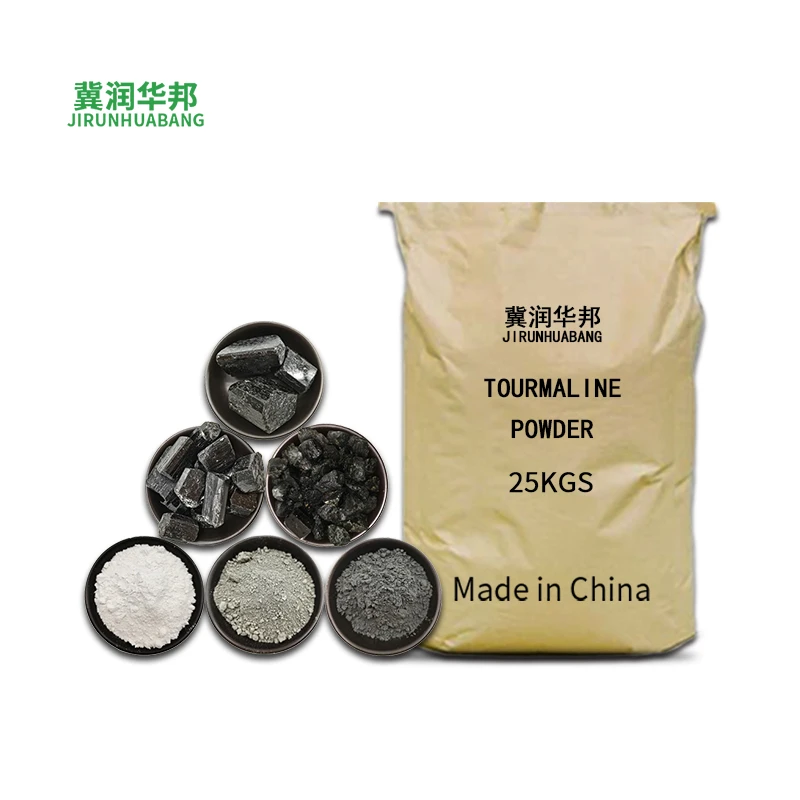
The manufacturing process itself is where expertise truly comes into play. Industrial-scale production of zeolites typically involves several critical stages synthesis, activation, and post-treatment. During the synthesis phase, raw materials such as silica and alumina are subjected to precise conditions to form the zeolite crystal structure. This phase requires expert knowledge of hydrothermal techniques and precise monitoring of variables like temperature and pressure to ensure optimal crystal growth.
Activation entails transforming the synthesized zeolite into a highly porous material. This is often achieved through calcination, where the material is heated to remove any organic templates used in synthesis. Expertise in thermal decomposition and process control is essential to uphold the material's structural integrity and achieve desired porosity. Finally, post-treatment processes may involve ion-exchange procedures or modification with functional agents to tailor the zeolite for specific industrial functions.
Quality assurance throughout the manufacturing process cannot be overstated. Certification by international standards such as ISO 9001 ensures adherence to quality management principles and continuous improvement. Implementing rigorous testing protocols to evaluate parameters like surface area, pore size distribution, and ion-exchange capacity is essential for approving batches of zeolites for sale.
zeolite factory
Equally important is fostering innovation within the factory's R&D department. Investigating novel synthesis methods or the development of new zeolite types can offer significant competitive advantages. Collaborating with academic institutions or participating in industry consortiums can aid in staying abreast of emerging trends and technological advancements.
The economic viability of a zeolite factory hinges on its ability to adapt to market demands dynamically. This includes diversifying the product range to cater to different sectors, such as providing customized zeolites for specific applications in agriculture or renewable energy. Exploring opportunities in rapidly growing markets, such as water treatment or carbon capture technologies, reinforces the factory's market position and ensures sustained growth.
Sustainability is no longer an optional consideration but a prerequisite in modern manufacturing. Zeolite factories excel when they incorporate sustainable practices into their operations. Utilizing green chemistry principles in synthesis, optimizing energy consumption, and reducing waste through recycling and reusing materials are all elements that enhance a factory's environmental stewardship.
In an industry characterized by precision and performance, trustworthiness is built on transparency and reliability. Establishing an informative, user-friendly web presence that details the factory's processes, certifications, and quality commitments is invaluable for building client confidence. Publishing white papers or case studies that showcase successful applications of the factory's products further cements its reputation as a reliable and knowledgeable partner in the zeolite industry.
The journey of running a zeolite factory is a testament to the interplay of innovation, expertise, and commitment to quality. By emphasizing these core values, manufacturers not only advance their businesses but also contribute positively to a more sustainable industrial future.